SICK Setup
UI/UX Design, Web Design
UI/UX Design, Web Design
2023
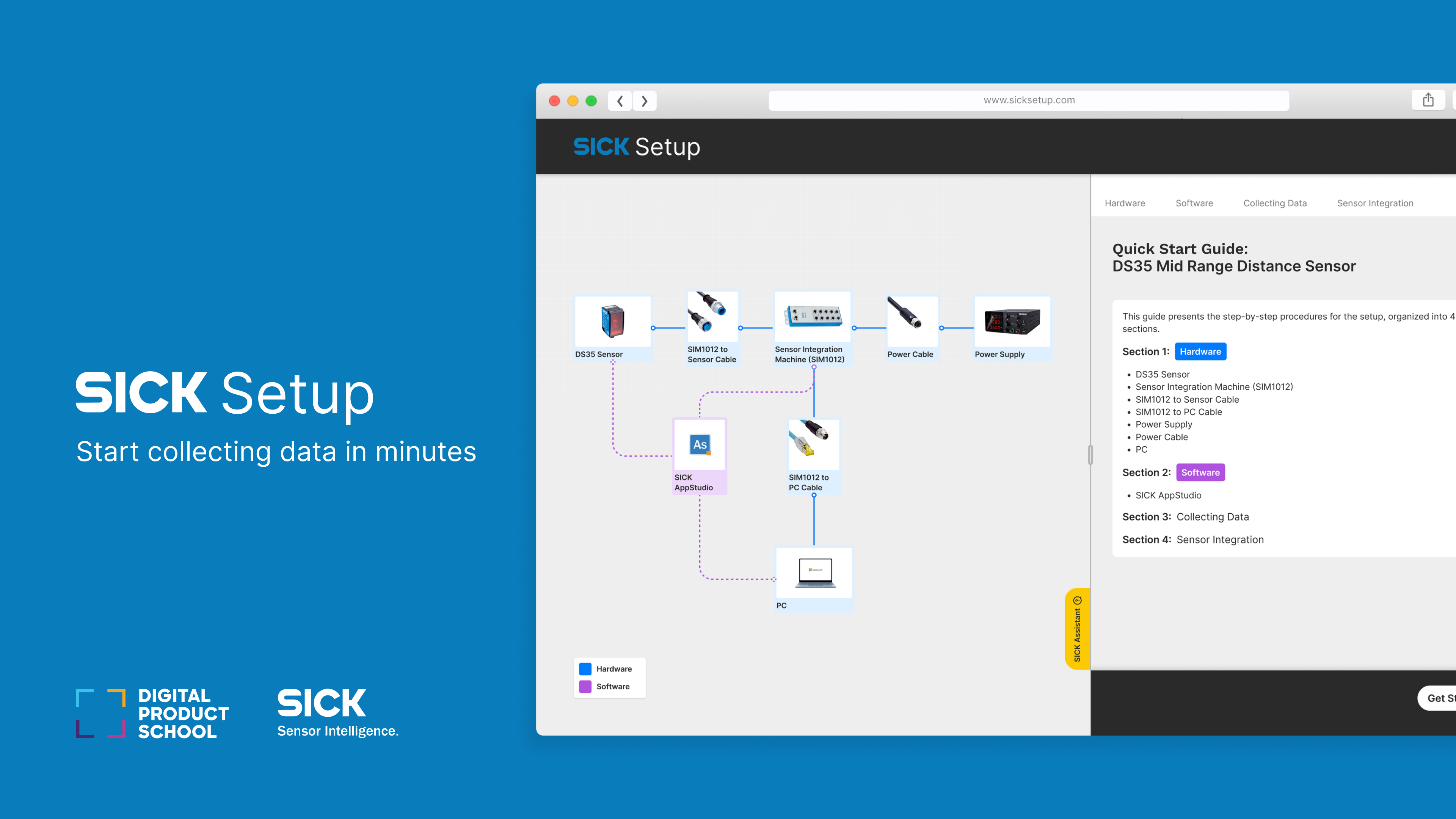
Cross-functional Team
🇧🇷 Bruno Teixeira Botelho - Product Manager
🇹🇭 Artipon Deewongkij - Interaction Designer
🇮🇳 Praveen Mohandas - AI Engineer
🇩🇪 Jago Wahl-Schwentker - Software Engineer
🇪🇬 Mohamed Maged Elgamal - Software Engineer
Timeline: May - July 2023 (3 months)
🇧🇷 Bruno Teixeira Botelho - Product Manager
🇹🇭 Artipon Deewongkij - Interaction Designer
🇮🇳 Praveen Mohandas - AI Engineer
🇩🇪 Jago Wahl-Schwentker - Software Engineer
🇪🇬 Mohamed Maged Elgamal - Software Engineer
Timeline: May - July 2023 (3 months)
Responsibilities
• Covering the entire design process, beginning with user interviews, market research, designing a product, and presenting to stakeholders
• Analyzing user behavior to acquire user insights, identify problems, and come up with innovative solutions
• Conducting product testing to identify problems and areas for improvement within the customer experience
• Collaborating closely with the product manager, software engineers, and AI engineers to ensure that the product meets user needs
• Covering the entire design process, beginning with user interviews, market research, designing a product, and presenting to stakeholders
• Analyzing user behavior to acquire user insights, identify problems, and come up with innovative solutions
• Conducting product testing to identify problems and areas for improvement within the customer experience
• Collaborating closely with the product manager, software engineers, and AI engineers to ensure that the product meets user needs
Background →
SICK is one of the world’s leading manufacturers of intelligent sensors and sensor solutions for industrial applications. With more than 50 subsidiaries, equity investments, and numerous agencies, SICK maintains a presence around the globe. SICK has almost 12,000 employees worldwide and generated a group revenue of around EUR 2.2 billion in the 2022 fiscal year.
SICK is one of the world’s leading manufacturers of intelligent sensors and sensor solutions for industrial applications. With more than 50 subsidiaries, equity investments, and numerous agencies, SICK maintains a presence around the globe. SICK has almost 12,000 employees worldwide and generated a group revenue of around EUR 2.2 billion in the 2022 fiscal year.
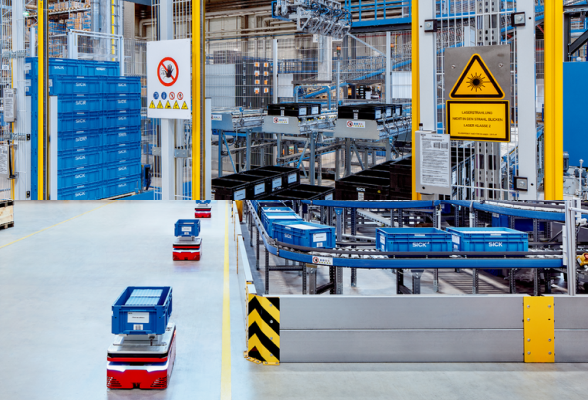
Problem Space →
“Wouldn't it be great if an innovator could develop new industrial solutions with the same ease and simplicity as DIY communities?”
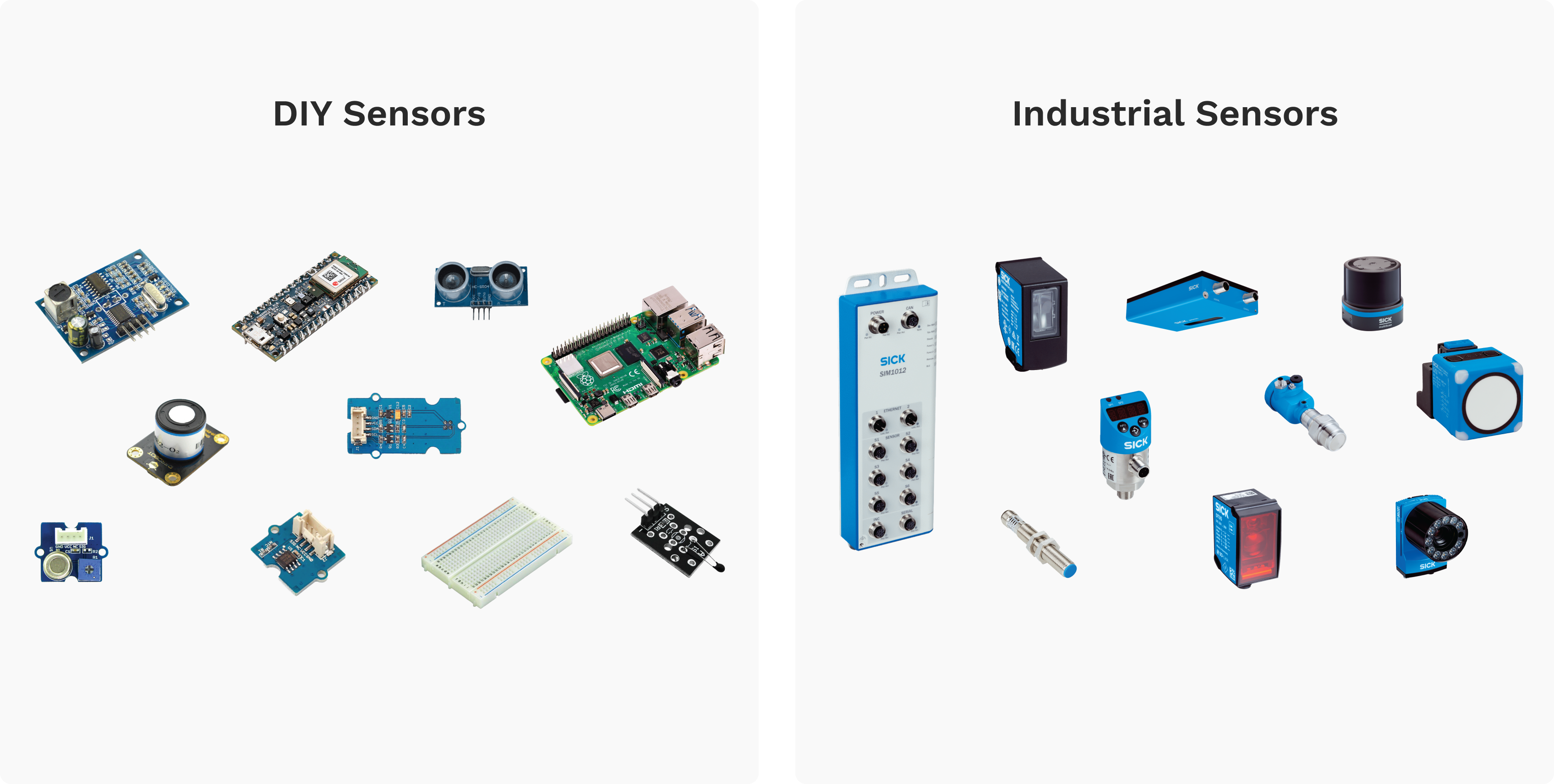
Week 1-4: Discover →
To gain a clear understanding of the problem and its users, a discovery phase was essential. This phase involved exploring the problem space, generating ideas, and uncovering innovative opportunities that align with user needs.
To achieve this goal, I employed a mixed methods approach that encompassed various research methods, including:
• Users interviews
• User journeys
• Comparing DIY Communities and Industrial Sensors
Users Interviews
We conducted user interviews with a total of 13 participants, who were divided into 4 groups: Startups, Startup Supporters, SICK Team and DIY communities.
These user interviews took place at the Munich Urban Colab and lasted for 1-2 hours each. The main objective was to deep dive into the prototyping process, gaining insights into user behaviors, goals, and frustrations.
We conducted user interviews with a total of 13 participants, who were divided into 4 groups: Startups, Startup Supporters, SICK Team and DIY communities.
These user interviews took place at the Munich Urban Colab and lasted for 1-2 hours each. The main objective was to deep dive into the prototyping process, gaining insights into user behaviors, goals, and frustrations.

Startup Phase
Based on the insights gathered from user interviews, we were able to identify 6 distinct phases that startups go through. Each phase comes with its unique requirements and motivations for selecting sensors to use in their prototypes.
Our participant, Leox from Oliver Robotics, not only undertook a journey that spanned all these phases but also offered us a comprehensive overview of how startups operate. His valuable insights and information have greatly enriched our understanding.
![]()
Based on the insights gathered from user interviews, we were able to identify 6 distinct phases that startups go through. Each phase comes with its unique requirements and motivations for selecting sensors to use in their prototypes.
Our participant, Leox from Oliver Robotics, not only undertook a journey that spanned all these phases but also offered us a comprehensive overview of how startups operate. His valuable insights and information have greatly enriched our understanding.

Sensor Selection Factors
After analyzing the interview data, we uncovered distinct patterns. In the proof of concept phase, startups show heightened concern for sensor limitations and compatibility, emphasizing easy integration with other sensors. Moving to the prototyping phase, the focus shifts to scalability, sensor performance, and safety considerations.
Throughout both startup phases, time efficiency remains a priority in sensor implementation, and the availability of comprehensive documentation and real-world project examples using these sensors holds significant value.


User Journey
We noticed a common pattern in how users go through the process, what they learn, and where they face issues. It's clear that they all struggle with a shared problem related to using industrial sensors.
The most frustrating aspect of their experience occurs during sensor setup. Users struggle to find the quick start guide and end up spending time reading through hundreds of documents. Unfortunately, they still can't determine how to set up the sensors in the end.
![]()
We noticed a common pattern in how users go through the process, what they learn, and where they face issues. It's clear that they all struggle with a shared problem related to using industrial sensors.
The most frustrating aspect of their experience occurs during sensor setup. Users struggle to find the quick start guide and end up spending time reading through hundreds of documents. Unfortunately, they still can't determine how to set up the sensors in the end.
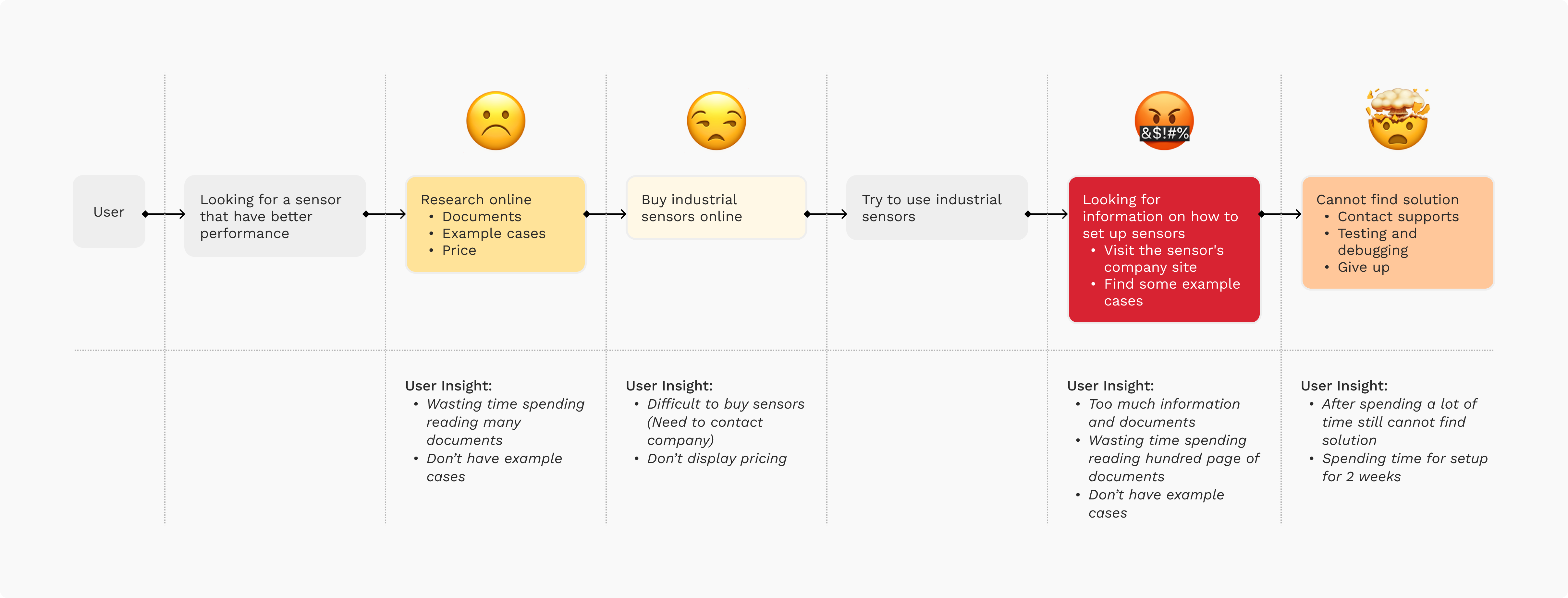
Comparing DIY Communities and Industrial Sensors
DIY Communities
We delved into both DIY communities and the world of industrial sensors, revealing intriguing differences. Within DIY communities, buying sensors is effortless, accessible not only through official websites but also popular platforms like Amazon and Alibaba. These communities have strong and lively interactions, with supportive members, step-by-step guides, and even sharing code for quick integration. In addition, real-world projects showcasing sensor use are also widespread.
![]()
We delved into both DIY communities and the world of industrial sensors, revealing intriguing differences. Within DIY communities, buying sensors is effortless, accessible not only through official websites but also popular platforms like Amazon and Alibaba. These communities have strong and lively interactions, with supportive members, step-by-step guides, and even sharing code for quick integration. In addition, real-world projects showcasing sensor use are also widespread.

Industrial Sensors
On the other hand, Purchasing industrial sensors online is complex, often lacking transparent pricing, necessitating quotation requests and patient waiting. Furthermore, the accompanying documentation proves cumbersome, spanning hundreds of pages with information not always pertinent to startups aiming for efficient sensor implementation. They have some communities as well, but they are not as strong or proactive.
![]()
On the other hand, Purchasing industrial sensors online is complex, often lacking transparent pricing, necessitating quotation requests and patient waiting. Furthermore, the accompanying documentation proves cumbersome, spanning hundreds of pages with information not always pertinent to startups aiming for efficient sensor implementation. They have some communities as well, but they are not as strong or proactive.

DIY Sensor Setup

Industrial Sensors Setup
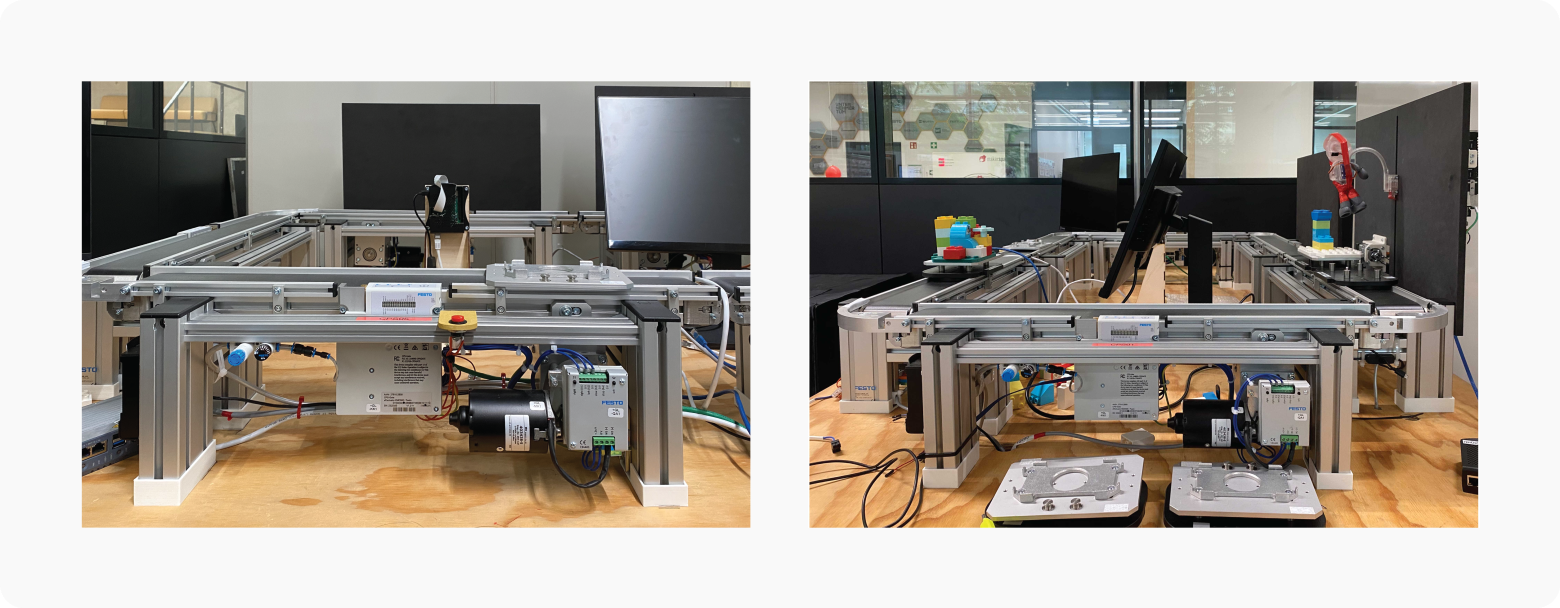
Week 5: Define & Ideation →
As we build upon the insights gained in the discovery phase, the define phase comes into play. During this phase, we've delved into challenges and generated ideas. Now, we're using this foundation to comprehend the problem and its users, setting the stage for creative solutions.
In this phase, we're proactively utilizing a diverse range of methods to generate fresh ideas, including:
• Personas
• How Might We Questions (HMW)
Persona
These personas are built upon the insights gathered during the discovery phase, drawing from user interviews, observations, and data analysis. Each persona encapsulates essential characteristics, behaviors, goals, and pain points of the user group it represents.
We've categorized our personas into 2 distinct types:
Type 1:
Innovator in the Proof of Concept Phase
• Upgrading to industrial sensors for improved precision and reliability.
• Focused on enhancing performance during the early stages.
• Upgrading to industrial sensors for improved precision and reliability.
• Focused on enhancing performance during the early stages.

Type 2: Innovator in Prototyping Phase
• Creating prototypes with scalability in mind for future product development.
• Exploring ways to ensure seamless transition from prototype to final product.
• Creating prototypes with scalability in mind for future product development.
• Exploring ways to ensure seamless transition from prototype to final product.
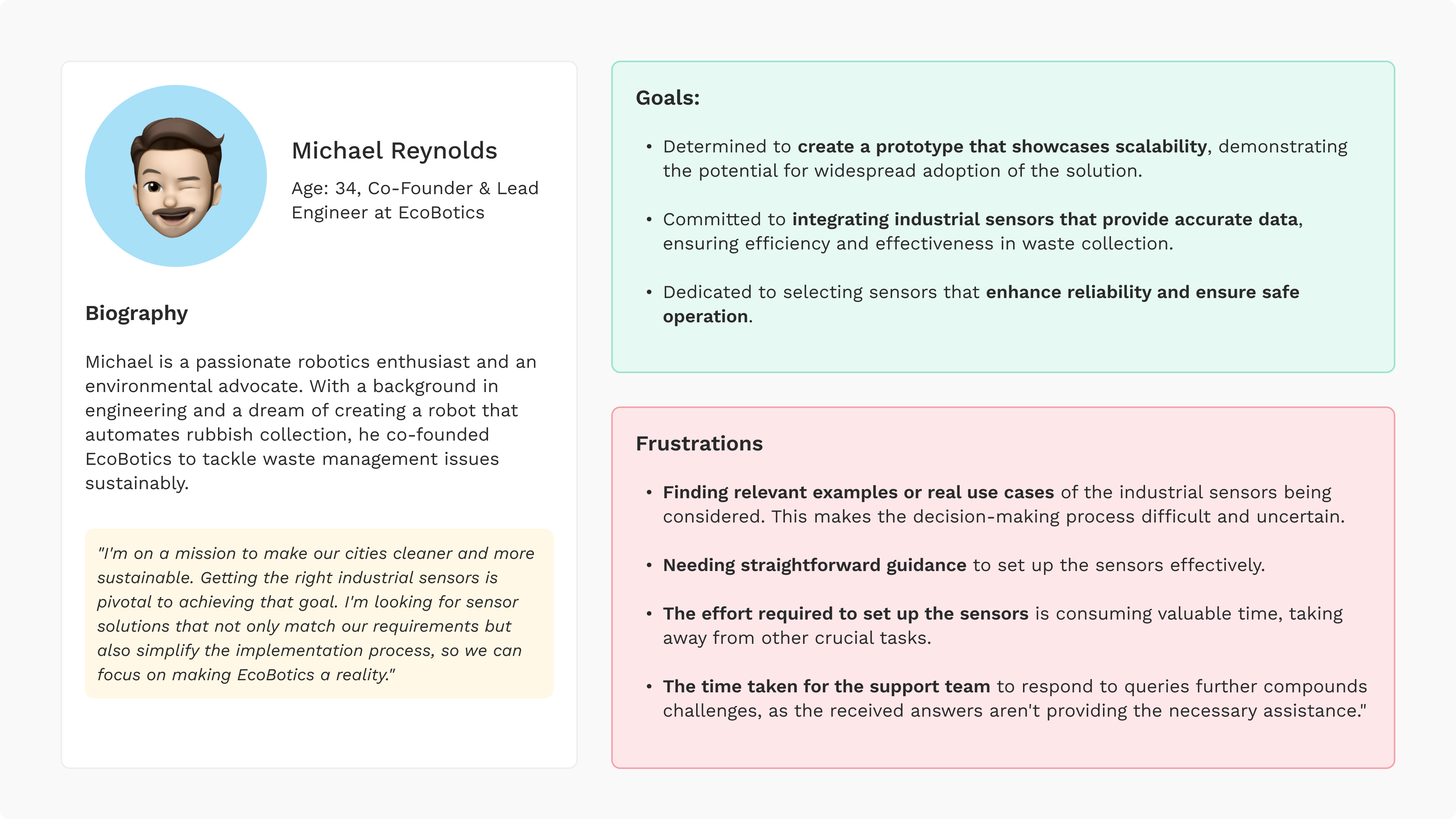
HMW Questions
We dedicated time to review the notes and insights from the interviews I conducted, transforming the identified pain points into HMW questions. These questions were then organized into categories, and our team collectively voted to pinpoint the most relevant queries aligned with our persona. Through this process, we effectively prioritized the issues based on the team's consensus.
Finally, our team reached a decision and chose to focus on the following question:
“How might we help startups get started quickly with industrial-grade sensors?”
We dedicated time to review the notes and insights from the interviews I conducted, transforming the identified pain points into HMW questions. These questions were then organized into categories, and our team collectively voted to pinpoint the most relevant queries aligned with our persona. Through this process, we effectively prioritized the issues based on the team's consensus.
Finally, our team reached a decision and chose to focus on the following question:
“How might we help startups get started quickly with industrial-grade sensors?”
![]()
After formulating the HMW question, we kicked off the ideation process with brainstorming. Our team had insightful discussions on user-centered solutions to address the problem. Post-discussion, we used the Impact Effort Matrix to help us decide on the best solution.
Our team decided to develop a platform that enabled users to effortlessly manage and execute the necessary tasks for setting up sensors. Additionally, we're creating an AI chatbot that will swiftly guide innovators through documentation, offering quick solutions tailored to their queries about the components.
Brainstorming
![]()
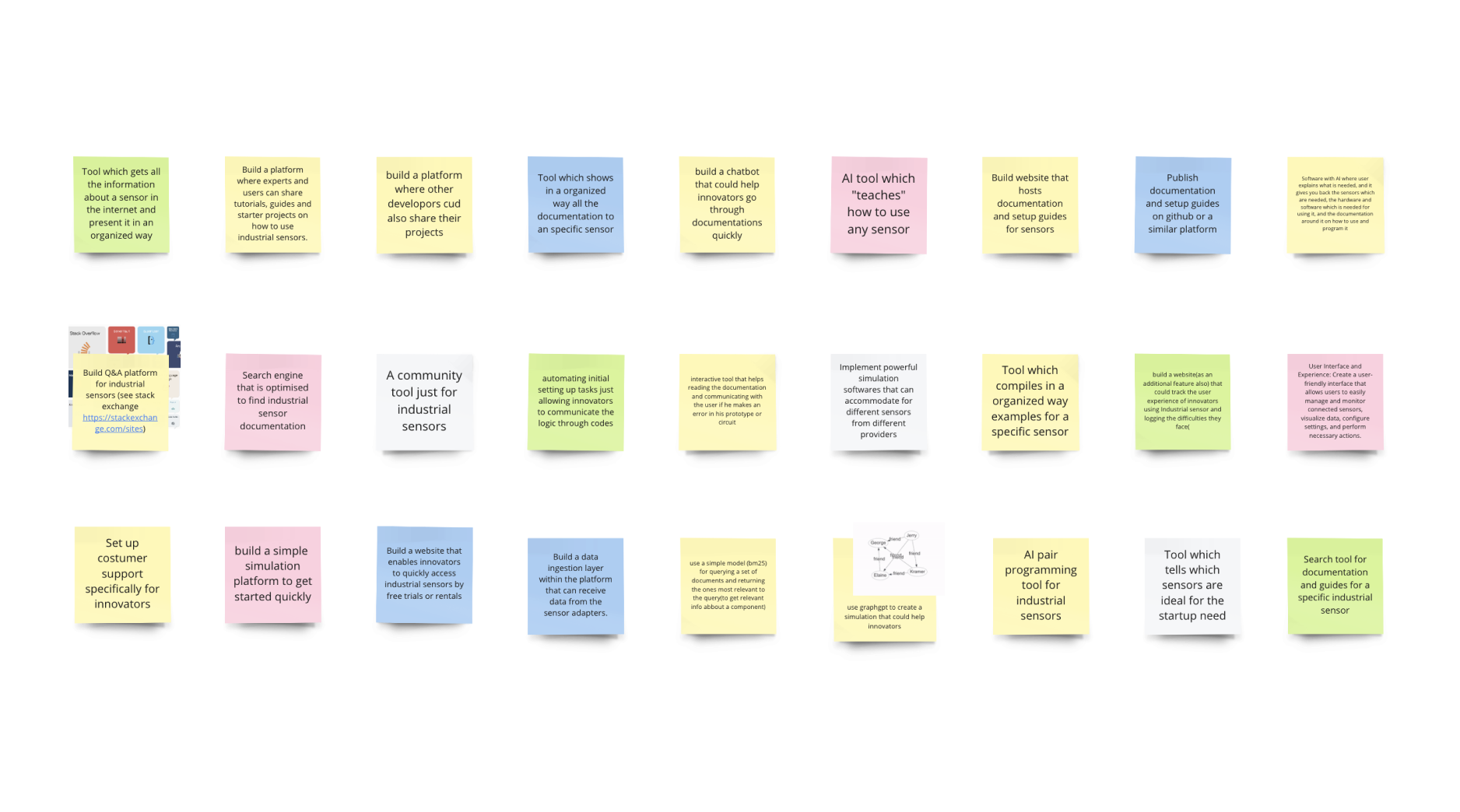
Impact Effort Matrix
![]()

Week 6-12: Development & Iterations →
We embarked on the implementation phase with weekly iteration cycles. My responsibilities during this phase encompassed:
• Engaging in a 'Services Safari' to experience SICK's offerings as a user, traversing user journeys, identifying pain points, and discovering opportunities for enhanced user experiences (Note: We encountered a delay in receiving the sensors as initially planned).
• Conducting user tests utilizing diverse design solutions, including Story Map and Prototyping.
• Validating initial wireframes and preparing them for handoff to the development team for implementation.
• Creating hi-fi designs and developing a comprehensive design system.
Services Safari
We gained substantial insights from our own hands-on experience with industrial sensors. We discovered an abundance of documentation, which often proved to be challenging to comprehend. Additionally, while there was a support forum available for inquiries, it was not notably active, leading to delays of days in receiving responses that weren't very helpful.
The insights we gathered align with the user journey, spanning from the initial purchase of a Sick sensor to its setup and eventual integration into a prototype.
We gained substantial insights from our own hands-on experience with industrial sensors. We discovered an abundance of documentation, which often proved to be challenging to comprehend. Additionally, while there was a support forum available for inquiries, it was not notably active, leading to delays of days in receiving responses that weren't very helpful.
The insights we gathered align with the user journey, spanning from the initial purchase of a Sick sensor to its setup and eventual integration into a prototype.
• Purchasing a SICK sensor:
- Buying a sensor from Sick is challenging as it lacks fundamental product information such as price and delivery date.
- The website isn't user-friendly.
- Users must create an account to access pricing and delivery details.
- Finding Sick products on external platforms is less straightforward compared to easily available Arduino sensors from platforms like Alibaba or Amazon.
- Buying a sensor from Sick is challenging as it lacks fundamental product information such as price and delivery date.
- The website isn't user-friendly.
- Users must create an account to access pricing and delivery details.
- Finding Sick products on external platforms is less straightforward compared to easily available Arduino sensors from platforms like Alibaba or Amazon.

• Hardware:
- The hardware's preparation for use doesn't align with its higher price point (for instance, the power cable isn't ready for direct connection to a power supply; users must strip the wires themselves).
- Basic information for activating the SIM and Sensor is missing. Connecting it to the Power Supply became a challenge without internal support from Sick. Connecting the 4 wires from the Power Cable to the Power Supply wasn't explained in the documentation.
- Finding a computer with a connector like RJ45 is difficult due to its rarity.
- The hardware's preparation for use doesn't align with its higher price point (for instance, the power cable isn't ready for direct connection to a power supply; users must strip the wires themselves).
- Basic information for activating the SIM and Sensor is missing. Connecting it to the Power Supply became a challenge without internal support from Sick. Connecting the 4 wires from the Power Cable to the Power Supply wasn't explained in the documentation.
- Finding a computer with a connector like RJ45 is difficult due to its rarity.

• Software:
- There are multiple software options such as AppManager, AppStudio, and AppPool, but their distinctions are unclear.
- The apps have an outdated appearance and run slowly. Users need both an account and a license, which takes time and support from the team.
- Setting up the IP address using the software is challenging, and it's almost impossible without Sick's internal support.
- There are multiple software options such as AppManager, AppStudio, and AppPool, but their distinctions are unclear.
- The apps have an outdated appearance and run slowly. Users need both an account and a license, which takes time and support from the team.
- Setting up the IP address using the software is challenging, and it's almost impossible without Sick's internal support.

User Testing
We collaborated within an agile framework and engaged in weekly product testing. Embracing early feedback in the design process, we streamlined our product iteration for greater efficiency.
8 Prototype Iterations
During the testing phase, our attention was directed towards assessing the usability of product features, user journeys, and user preferences for visual aesthetics. We also uncovered certain design challenges.
We collaborated within an agile framework and engaged in weekly product testing. Embracing early feedback in the design process, we streamlined our product iteration for greater efficiency.
8 Prototype Iterations
12 User Testing Sessions
During the testing phase, our attention was directed towards assessing the usability of product features, user journeys, and user preferences for visual aesthetics. We also uncovered certain design challenges.
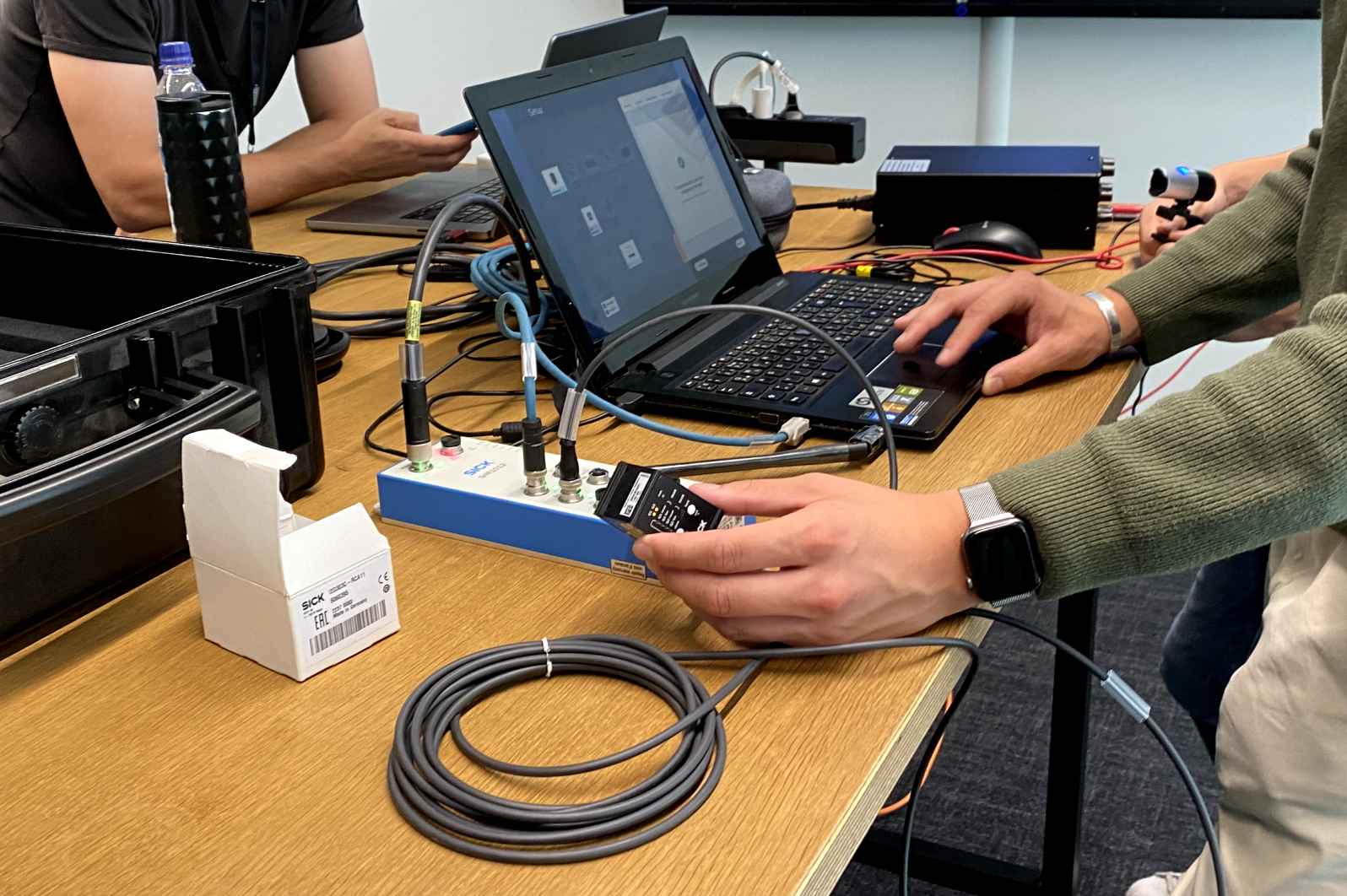









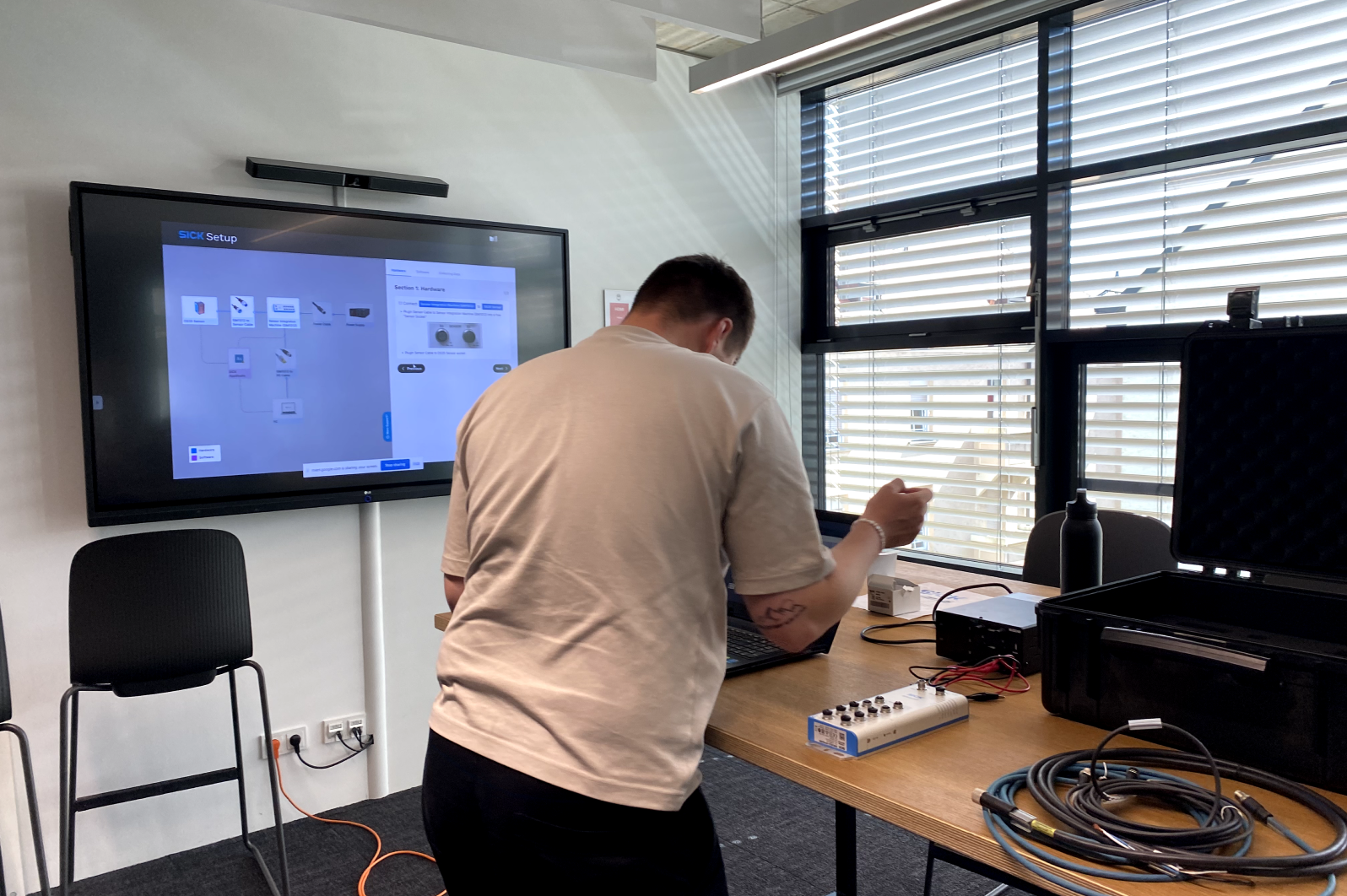

Exploration 1
We first designed our step-by-step guide by providing all the necessary text for users, displaying it as a listed series of steps.
However, after testing it with users, we discovered that there was too much information for them to digest, and they expressed a reluctance to read through all the text.
We first designed our step-by-step guide by providing all the necessary text for users, displaying it as a listed series of steps.
However, after testing it with users, we discovered that there was too much information for them to digest, and they expressed a reluctance to read through all the text.
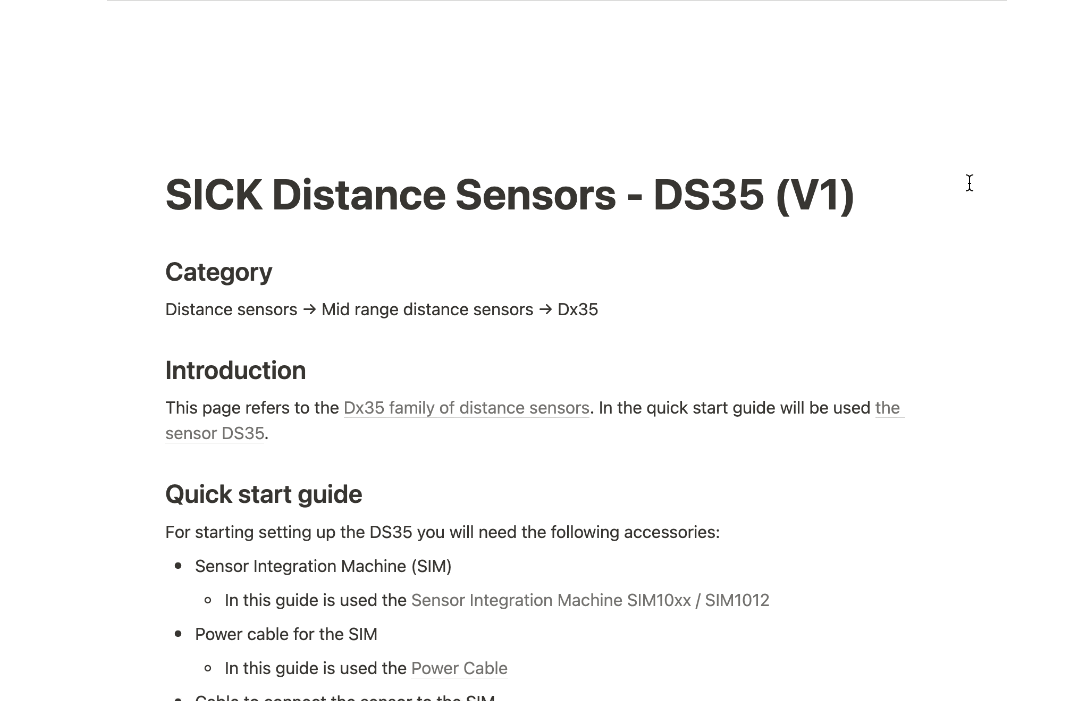
Exploration 2
To address this, we decided to incorporate more pictures into the guide to enhance its visual appeal and aid users in following the steps.
This change resulted in significantly more positive feedback, with users finding the guide easier to comprehend and follow.
One crucial revelation came when we introduced an overall picture that depicted the necessary hardware and the cables required to connect to the power supply, SIM, and sensor. Users spent considerable time studying this picture, seeking to understand the hardware setup and the connections needed.
To address this, we decided to incorporate more pictures into the guide to enhance its visual appeal and aid users in following the steps.
This change resulted in significantly more positive feedback, with users finding the guide easier to comprehend and follow.
One crucial revelation came when we introduced an overall picture that depicted the necessary hardware and the cables required to connect to the power supply, SIM, and sensor. Users spent considerable time studying this picture, seeking to understand the hardware setup and the connections needed.
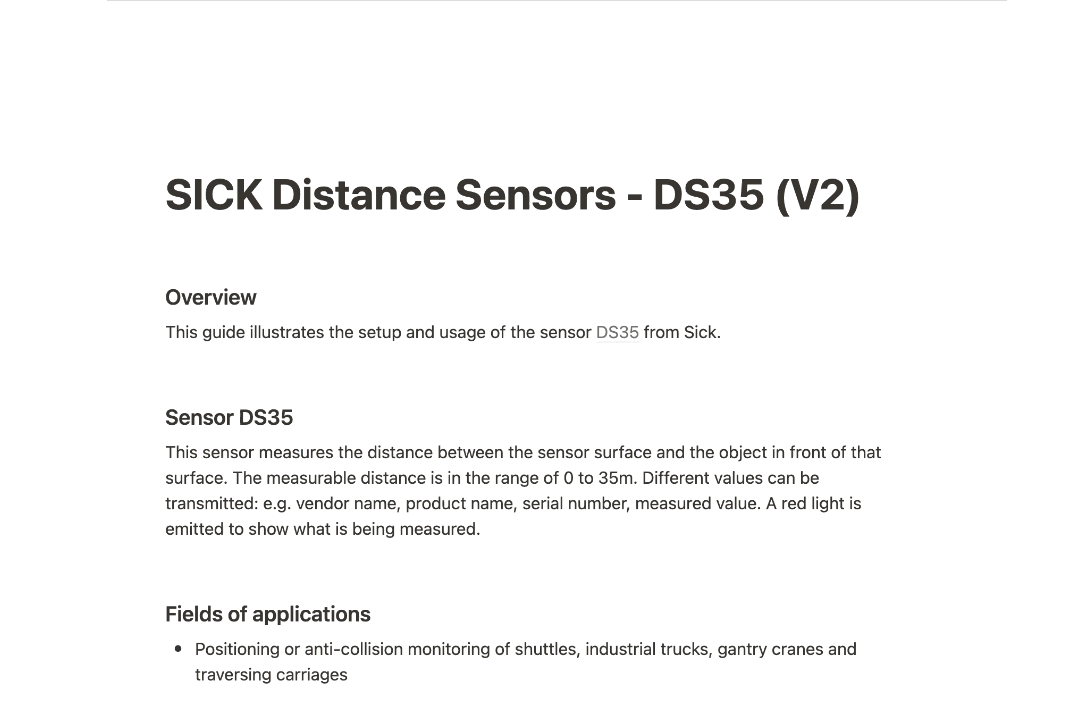
Exploration 3
Building upon this insight, we further improved the design by using diagrams to provide a visual representation of each step. This allowed users to grasp the specific actions required and which hardware components needed to be interconnected.
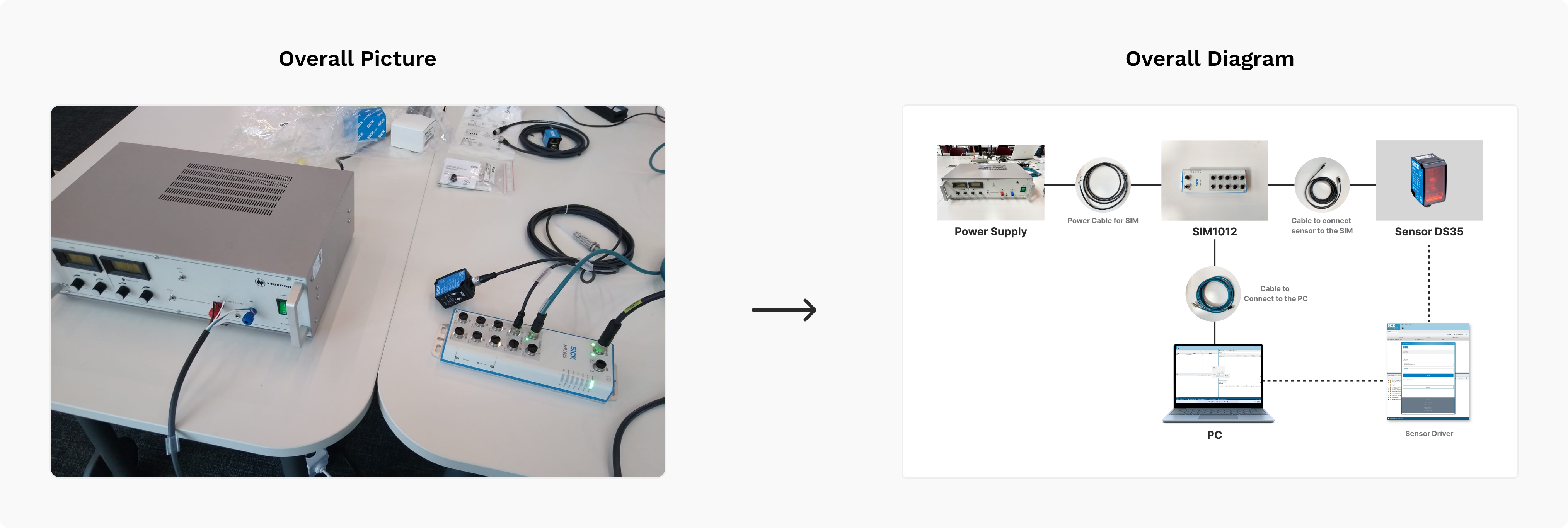
Alongside the diagrams, we incorporated additional detailed pictures and used colors to emphasize distinctions between hardware and software. Since setting up the sensors necessitated connecting all the hardware first and then configuring the software later, this approach proved highly effective.
Upon testing this enhanced design with users, we received overwhelmingly positive feedback, as the diagrams significantly aided users in comprehending the cable connections between hardware components and how software could interact with them through the cloud.
Upon testing this enhanced design with users, we received overwhelmingly positive feedback, as the diagrams significantly aided users in comprehending the cable connections between hardware components and how software could interact with them through the cloud.
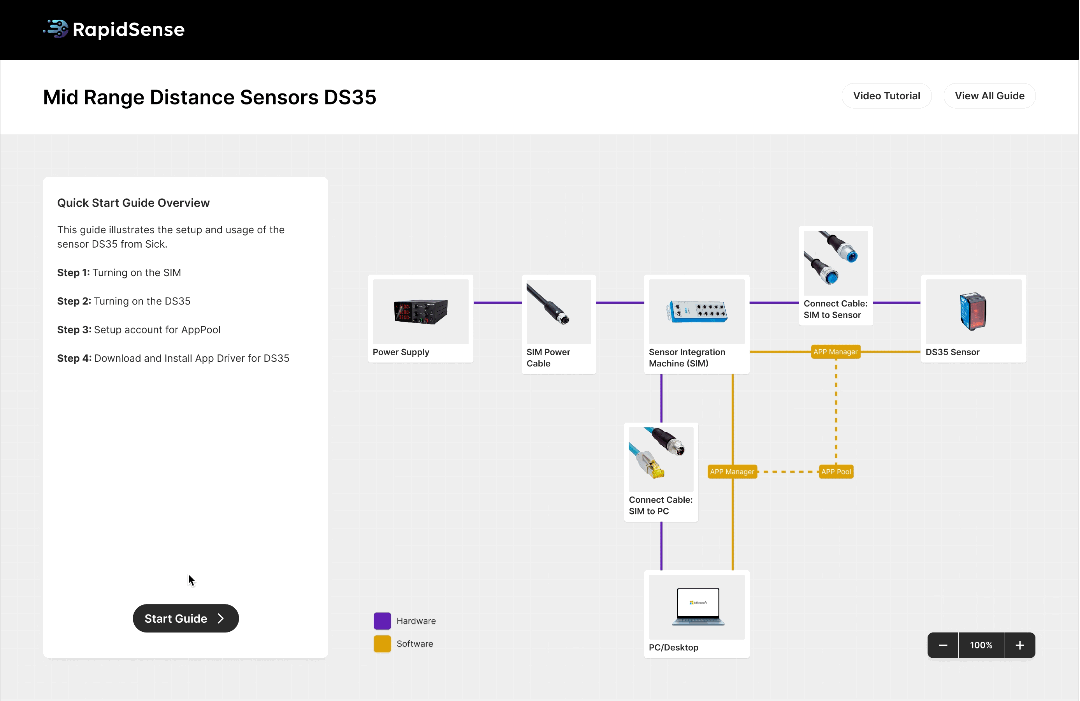
However, we did receive feedback that the step descriptions were too small and that there's a need to better connect the diagrams and step descriptions. Additionally, users pointed out that some steps contained multiple tasks, suggesting that dividing these tasks into fewer steps could be more helpful.
Exploration 4
In response to user feedback, we adjusted the design by enlarging step descriptions, emphasizing essential hardware and software elements in alignment with diagrams. Section tabs were introduced for users to skip sections if necessary, along with checkboxes on step details to track progress and prevent confusion about the current step.
During user testing, we encountered doubts about the website's credibility, as its name doesn't resemble SICK Company's official website. Regarding the diagram in the software section, some users became confused about which software to set up first and which one was for programming the sensors.
In response to user feedback, we adjusted the design by enlarging step descriptions, emphasizing essential hardware and software elements in alignment with diagrams. Section tabs were introduced for users to skip sections if necessary, along with checkboxes on step details to track progress and prevent confusion about the current step.
During user testing, we encountered doubts about the website's credibility, as its name doesn't resemble SICK Company's official website. Regarding the diagram in the software section, some users became confused about which software to set up first and which one was for programming the sensors.

Thanks to design iterations guided by user feedback,
users can now efficiently set up the sensors in just 15-30 minutes on average.
This has a profound impact on streamlining the process and enhancing overall productivity, from sensor setup to integration.
Final Solution →
Drawing insights from interviews, tests, and our own experiences, we have designed a solution to assist innovators in getting started with industrial sensors. Our solution is divided into 2 parts:
Firstly, we have developed a web-based platform that offers comprehensive, step-by-step instructions for setting up and utilizing sensors. We cover all elements, spanning from hardware and software configuration to data collection and sensor integration into prototypes. Additionally, we have introduced the SICK Assistant for instant support throughout the journey.
The second part of our solution involves the creation of the SICK Content Management System (CMS), which empowers the SICK team to seamlessly expand the guide to encompass various sensors. Leveraging the SICK CMS, they can effortlessly create, update, edit, or remove guide content.

SICK Setup ADS
SICK Setup
Within our case study, we present an illustrative example of the Quick Start Guide for the DS35 Mid Range Distance Sensor. This guide offers meticulous, step-by-step instructions to facilitate sensor setup and utilization. Covering all crucial aspects, innovators are guided through the process, starting from:
Throughout each of these steps, users have the added advantage of instant support through the SICK Assistant—an AI-powered support system that offers assistance 24/7.
Within our case study, we present an illustrative example of the Quick Start Guide for the DS35 Mid Range Distance Sensor. This guide offers meticulous, step-by-step instructions to facilitate sensor setup and utilization. Covering all crucial aspects, innovators are guided through the process, starting from:
- Hardware
- Software
- Collection Data
- Sensors Integration
Throughout each of these steps, users have the added advantage of instant support through the SICK Assistant—an AI-powered support system that offers assistance 24/7.
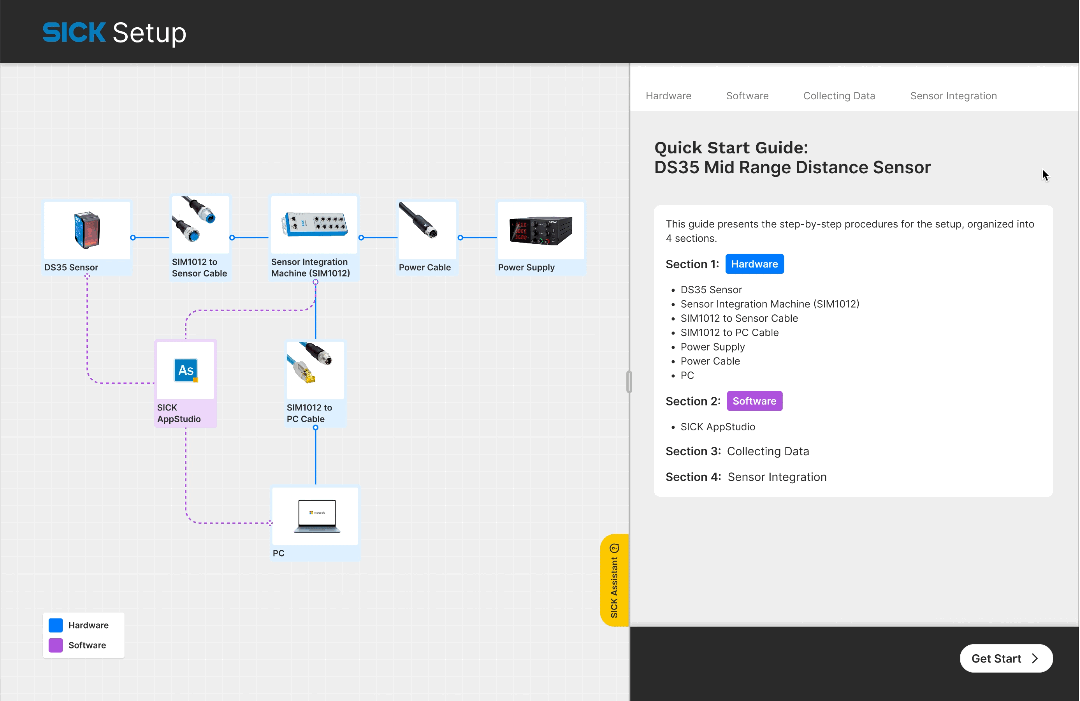
SICK Setup Kit
The comprehensive SICK Setup Kit equips you with all the essential components required for a seamless sensor installation and integration experience.
This kit includes:
With the SICK Setup Kit in hand, you're well-equipped to embark on your sensor integration journey, ensuring optimal performance and precise data collection.
The comprehensive SICK Setup Kit equips you with all the essential components required for a seamless sensor installation and integration experience.
This kit includes:
- DS35 Sensor
- Sensor Integration Machine (SIM1012)
- SIM1012 to Sensor Cable
- SIM1012 to PC Cable
- Power Cable
With the SICK Setup Kit in hand, you're well-equipped to embark on your sensor integration journey, ensuring optimal performance and precise data collection.


SICK Content Management System (CMS)
The CMS is key for the SICK team to expand the quick start guide's coverage to include a wide range of sensors, given SICK AG's extensive offering of over 40,000 sensor varieties. This scalability is essential for providing innovators with a comprehensive sensor setup experience in the long term.
The current version of the SICK CMS features a MVP, with plans to incorporate more functionalities in the future to further enhance the quick start guide.
The CMS is key for the SICK team to expand the quick start guide's coverage to include a wide range of sensors, given SICK AG's extensive offering of over 40,000 sensor varieties. This scalability is essential for providing innovators with a comprehensive sensor setup experience in the long term.
The current version of the SICK CMS features a MVP, with plans to incorporate more functionalities in the future to further enhance the quick start guide.
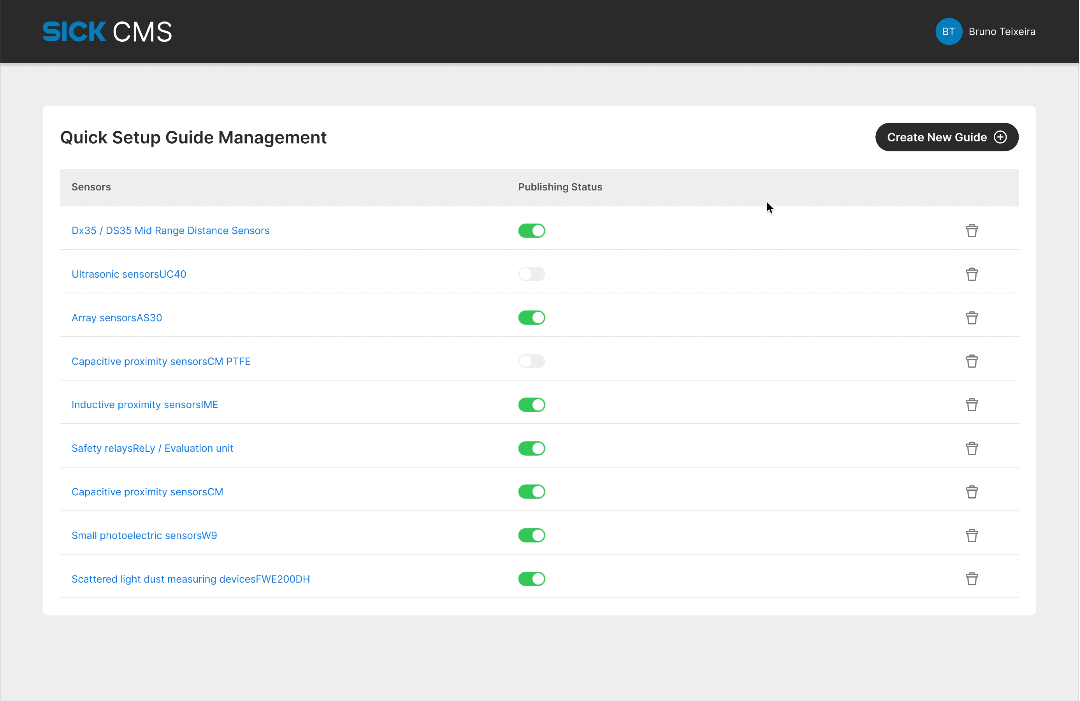
Key Takeaways →
01 - Just go with it! 👊
Initially, I worried about not having enough research for designing in this new field. Embracing an agile approach, I learned that perfection isn't necessary. Through user testing and feedback, I've realized it's okay if something doesn't work perfectly – I can keep moving forward and find better solutions.
02 - Disagree and commit 💪
During our team collaboration, we encountered differing viewpoints regarding the product's features. This practice ensured thorough consideration of perspectives and promoted collaboration and progress.
03 - Proactive and supporting the team 🙌
In a cross-functional team, you aren't confined to a single role; you're expected to be engaged and provide assistance wherever possible. Through my experience, I recognized the gaps in my team members' knowledge. For instance, I organized a knowledge-sharing session on the design system for my software engineer colleagues who specialized in the backend. This proactive approach ensured that our team received the necessary support and expertise.
Grateful to Digital Product School (DPS) and SICK Sensor Intelligence for this remarkable opportunity, alongside an incredible team! 😊 🎉 🍻
Grateful to Digital Product School (DPS) and SICK Sensor Intelligence for this remarkable opportunity, alongside an incredible team! 😊 🎉 🍻
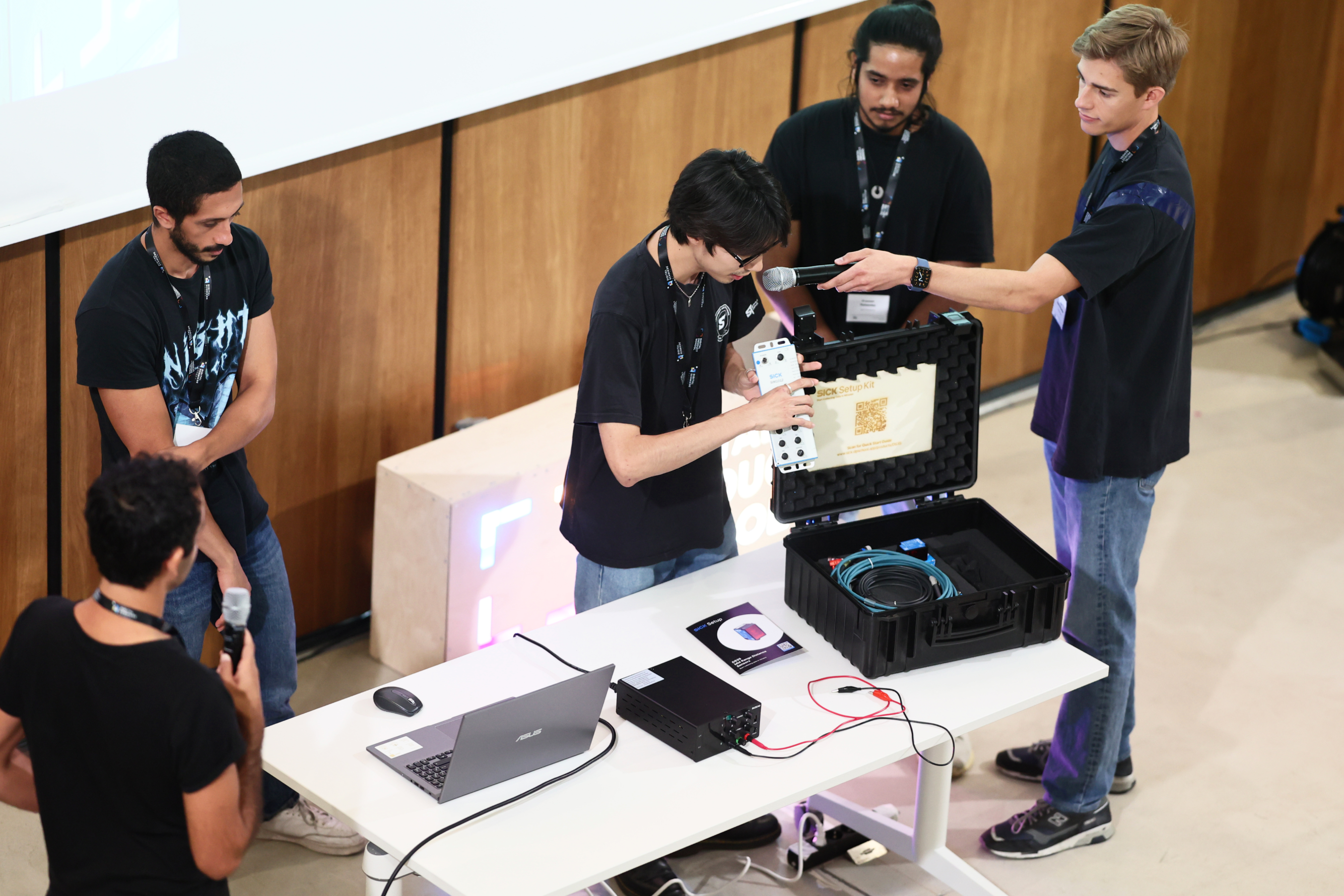
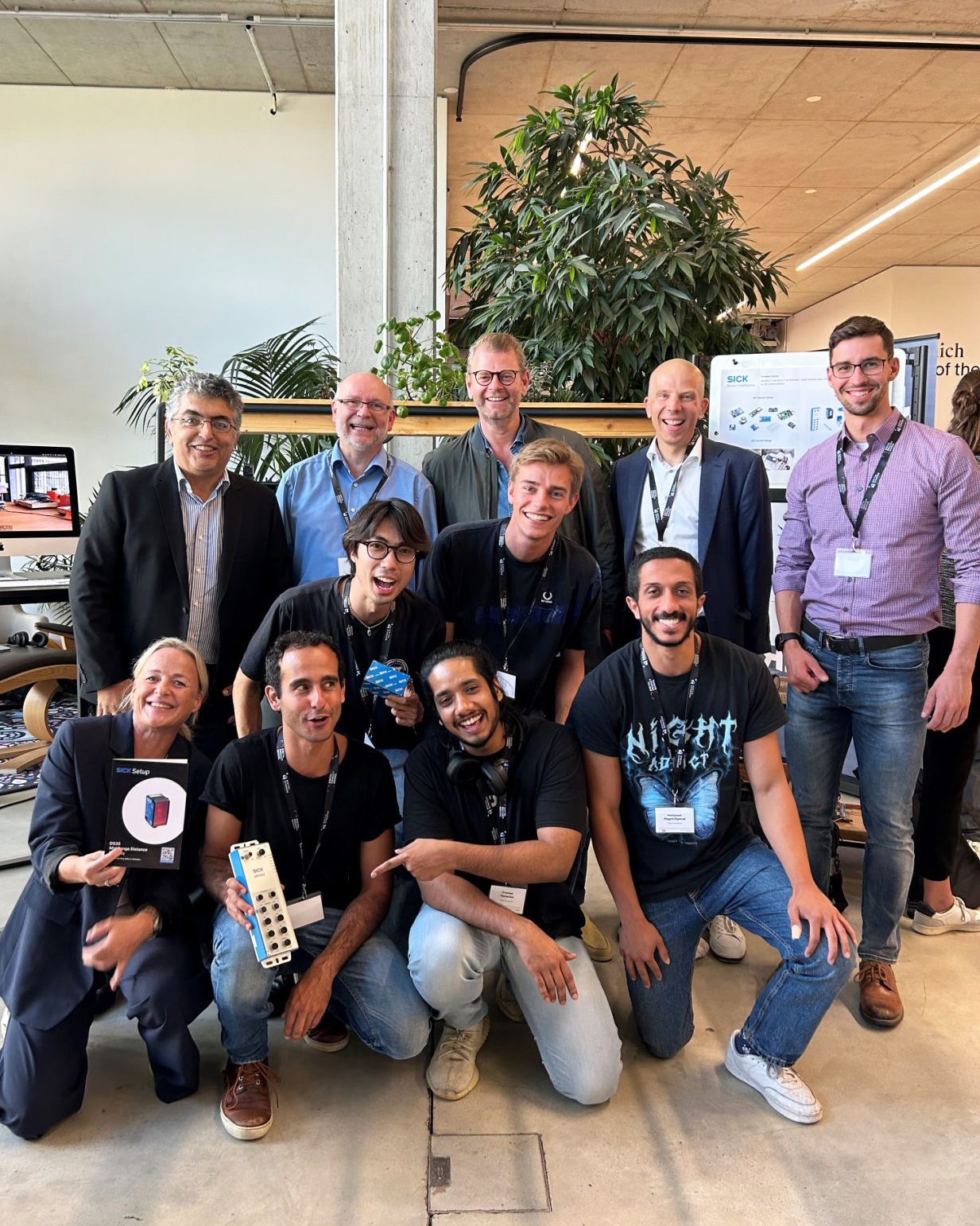

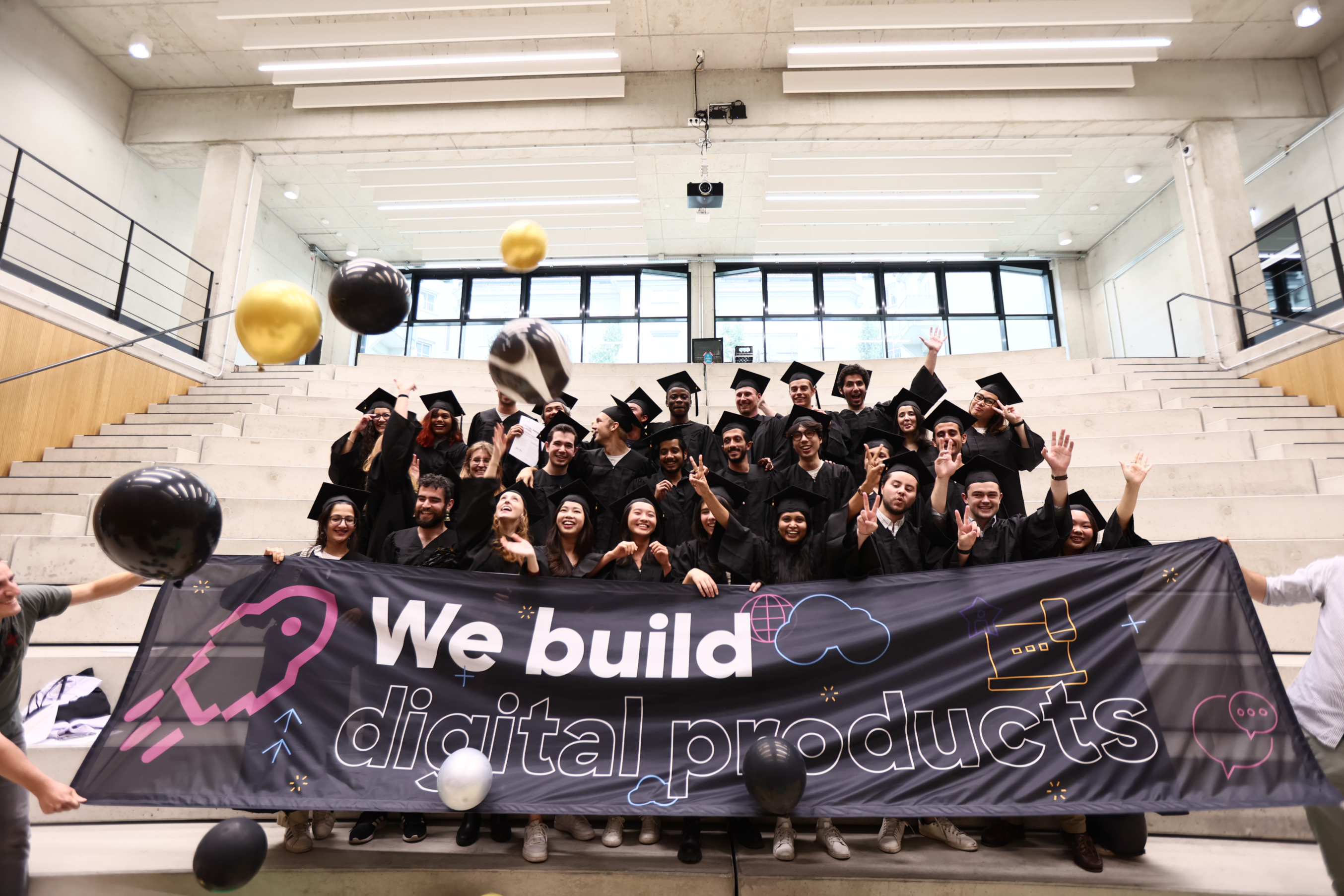
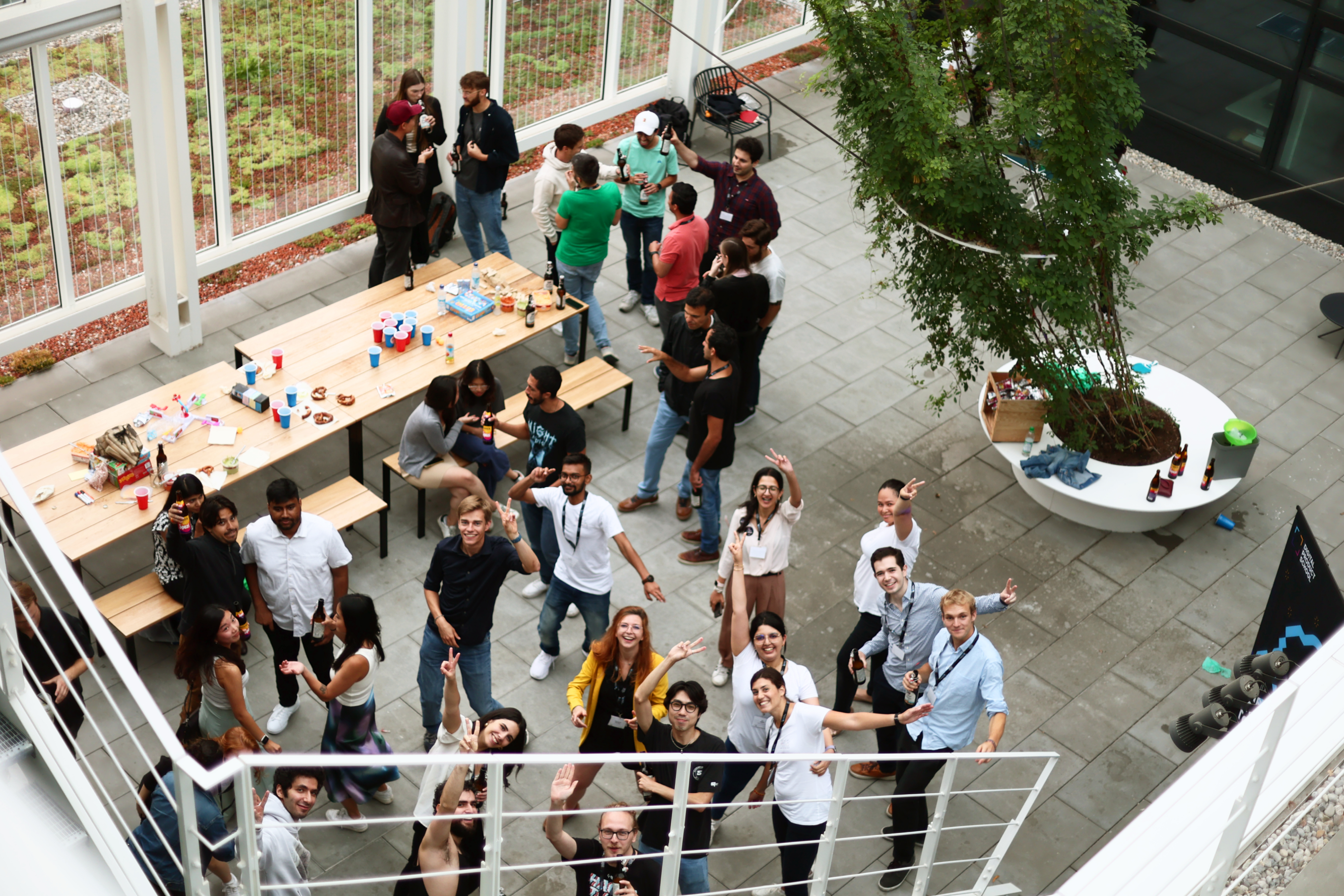